W assily Kandinsky famously said, “Colour is a power which directly influences the soul.” While the sight of a certain colour enlightens our minds, the tactile experience of holding such a monochromatic object touches our hearts. The texture of the surface, the play of the light, its translucency and thickness draws us deeply into its tantalising universe.
A remarkable collection of exquisite Chinese ceramics that had seemingly vanished since its acquisition from Edward T. Chow (1910-1980) in the 1960s is reappearing on the market for the first time in more than five decades. The collection comprises some of the rarest and most sought-after monochromes, charting the rise and fall of China’s dynasties from the Song to the Qing dynasties. Ahead of An Important European Collection of Chinese Ceramics - Acquired from Edward T. Chow on 9 April, we pay an ode to monochromes, to nature, and to colour.
Powder celadon
T he family of greens has been the backbone of Chinese monochromes since the dawn of ceramic production. The wide range of high-firing (over 1250°C) stoneware and porcelain celadon glazes resulted from various concentrations of iron oxide (0.5 to 2.5%) in moderate reduction with traces of titania (Nigel Wood, Chinese Glazes: Their Origins, Chemistry and Recreation, London, 1999, p. 165).
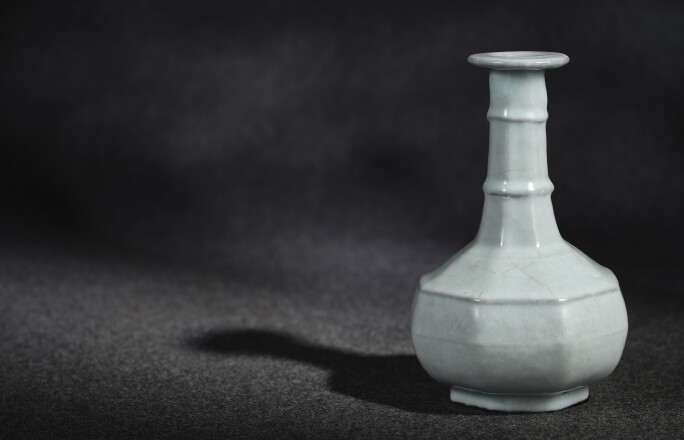
In the Southern Song dynasty (1127-1279), official guan kilns were established in Hangzhou to produce refined celadon wares with veined crackles that had once exclusively defined the esteemed Ru wares of the Northern Song (960-1127). The thick, unctuous glaze of jade-like quality was accomplished thanks to the gradual application of multiple layers, further enhanced by a network of distinct crackles provoked by a well-controlled cooling process. Reduction during firing was vital in achieving the signature cold bluish tone of guan wares, as well as the characteristic “purple mouths and iron feet” of the clay bodies exposed at the rims (ibid, pp. 161-165). However, oxidation was occasionally allowed at the later stages of firing and cooling. While the glaze would not be re-oxidised once it has melted, the shortened period of the reduction atmosphere could stop the unglazed clay from darkening completely, as observed on many excavated shards with an ochre body sandwiched by dark grey skins (Mou Baolei, Highlights of Celadon. Southern Song Official Kiln Tongjian, Hangzhou, 2017, p. 98).

In the Southern Song, guan vessels were already copied by the contemporaneous Longquan kilns in Zhejiang, and they continued to inspire the vast production of celadon wares in the Jingdezhen kilns throughout the Ming and Qing dynasties. The Qing court even sent guan vessels from the imperial collection to the Jiangxi manufactory for replication. These antiques were studied in detail and led to the development of attractive shades of celadon, such as douqing (pea green), of a bright sea-green colour, and fenqing (powder green), a pale bluish-green glaze.

Sweet white
W hite, a deceptively simple shade, warrants the highest level of skill and precision in the purity of the clay, potting, glazing and firing. Since its invention by Xing kilns in the Tang dynasty (618-907), white ceramics have enjoyed immense popularity and captivated connoisseurs for centuries. By the Song dynasty (960-1279), Ding kilns in the North and Jingdezhen in the South were dedicating considerable resources to manufacturing such elegant wares, producing dazzling white tones from warm ivory to cold blue-tinged qingbai.
In the early 15th century, potters at Jingdezhen developed a milky white glaze with a smooth surface, beautifully known as “sweet white” (tianbai). The semi-translucent glaze, combined with the finely potted vessels, reveals the exceptional craftsmanship and outstanding quality of materials at the imperial kilns. Nigel Wood describes this glaze in Chinese Glazes as “consisted almost entirely of glaze stone and contained little or no glaze ash” (op.cit., p. 66). The reduction or removal of glaze ash was the key to the brilliance of the tone, which differentiates tianbai from white glazes in other periods and from those used for contemporaneous blue-and-white porcelain.
Imperial yellow
T he “imperial yellow” glaze, a rich hue exclusively reserved for wares used in the inner court, was produced at the Jingdezhen kilns throughout the Ming dynasty (1368-1644). It was achieved by adding ferric oxide (3.5 %) to the lead silicate base, making this glaze a direct descendant of the yellow lead glazes of the Tang dynasty. Since the Hongzhi period (1488-1505), to produce such silky yellow wares the solution was poured onto the glazed porcelain before undergoing low-temperature firing in an oxidation atmosphere, resulting in a thick, even layer of amber tone with a glossy surface.

Such production of yellow wares continued well into the Qing dynasty (1644-1911). The traditional recipe, which produces rich, warm tones, was utilised alongside antimony yellow of pale, lemony tints imported from Europe by Jesuit artisans in the late 17th century (for example, see a pair of Yongzheng lemon-yellow cups in the Leshantang collection, lot 105).

Rose pink
C hinese potters have been devoted to the development of red porcelain pigments since the late Yuan dynasty. Still, nothing came close to the magnificence of rose pink, first introduced to China from Europe through Jesuit missionaries during the Kangxi period (1662-1722) (ibid, pp. 241-243). Numerous scientific experiments were conducted, and towards the end of the Kangxi period, around 1720, artisans developed an improved recipe of a matte ruby-pink enamel derived from colloidal gold combined with an admixture of opaque white lead arsenate. Production required blowing carefully through a silk gauze-covered bamboo tube on the biscuit before its second firing at a lower temperature (approx. 800 °C), resulting in a mottled effect. These technological achievements resulted in various irresistible shades, from soft peach pink to rich raspberry red, which revolutionised the porcelain colour palette.
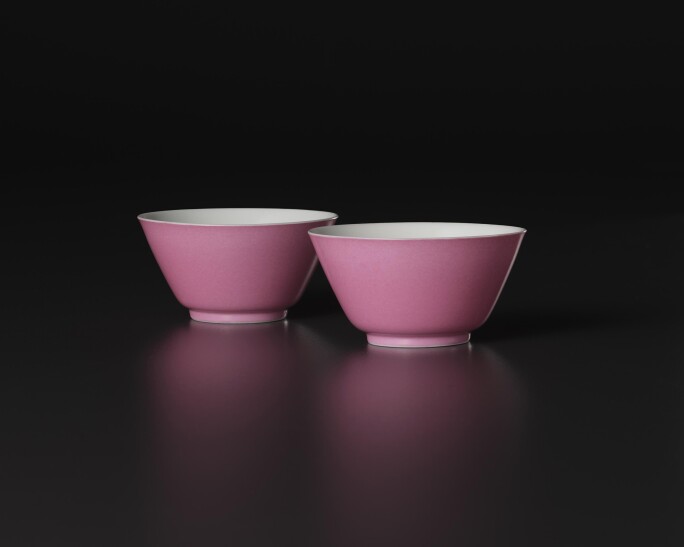
Since the late Kangxi period, an array of small, refined vessels characterised by fine potting and perfectly fired enamels of bright hues has been commissioned, but very few early examples are known. It was not until the Yongzheng (1723-1735) and Qianlong (1736-1795) periods that the low-fired ruby-red enamel became a more prominent feature in the repertoire of Chinese ceramics.